Plastic fabrication is the process of designing, producing, and assembling a product composed of plastic material or compounds. Given the enormous range of plastic-based products available today, several plastic fabrication techniques exist. Manufacturers should consider the benefits and drawbacks of each when fabricating specific designs. Plastic fabrication is currently very popular among manufacturers for its flexibility and affordability. It is a resilient and adaptable manufacturing process. Read More…
We are accomplished plastic fabricators. The usability of our products is unmatched. We offer a plethora of secondary services for optional features. All of engineers are extremely thorough when creating these plastics. Your satisfaction is essential to us. You can count on us to give you exactly what you are looking for. Give us a call today to learn more information!
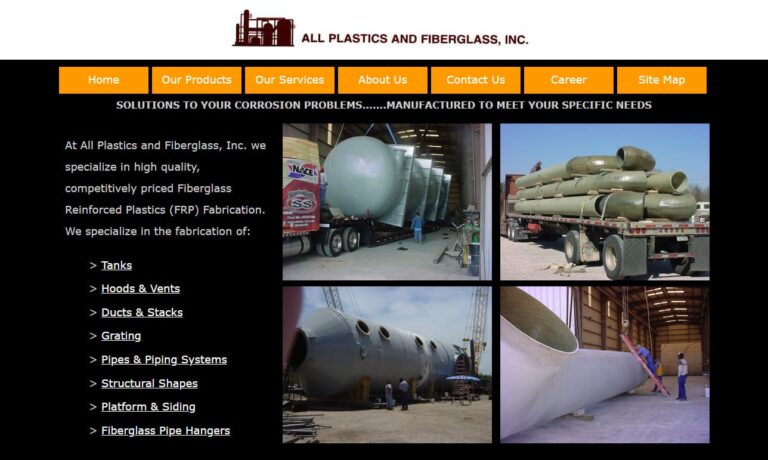
At Park Plastic Products our main focus is manufacturing custom fabricated tanks from polypropylene and co-polymer. Chemical rinse tanks, dip tanks, anodizing tanks, tank liners, air purification tanks, drip pans and custom rolled polypropylene tanks are available to be built to your size and specifications.
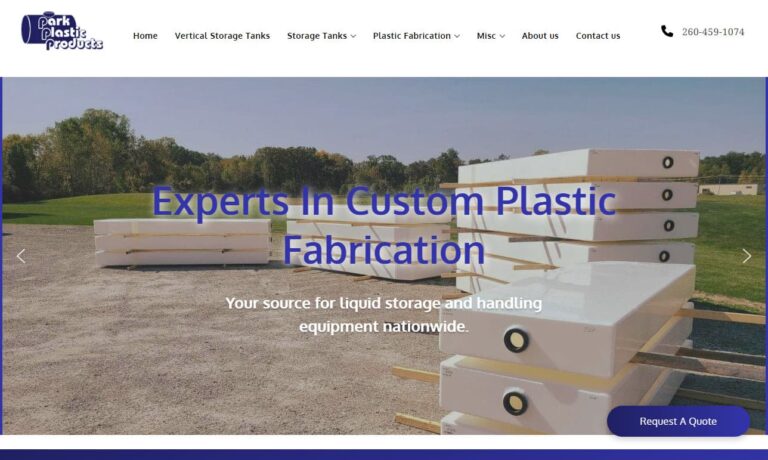
Experts in unique custom plastic extrusion products and complex secondary fabrications, Northland Plastics specializes in custom plastic profile extrusions such as extruded plastic tubing, rigid plastic profiles and flexible plastic profiles. Call Northland Plastics, Inc. for all your extrusion needs.
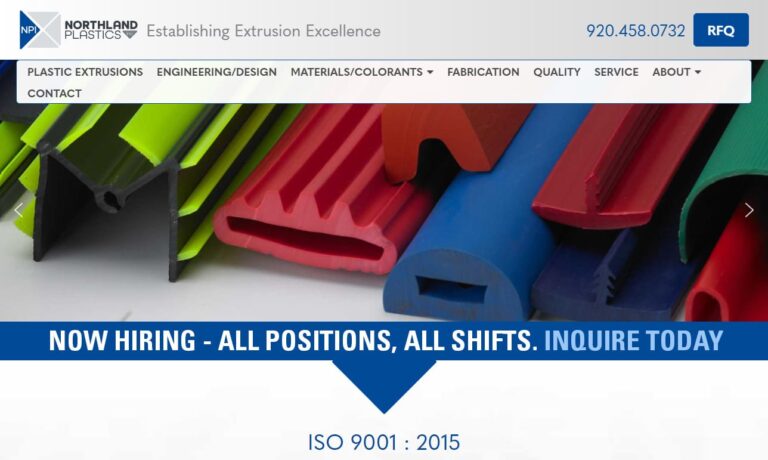
Thrust Industries is committed to quality in everything it does, from its technical knowledge to its customer service. As a leading plastic fabricator, the entire team at Thrust is devoted to developing high-quality solutions for your business and delivering them exactly when you need them. Thrust has served the needs of customers across the globe for over 3 decades— become one of them today.
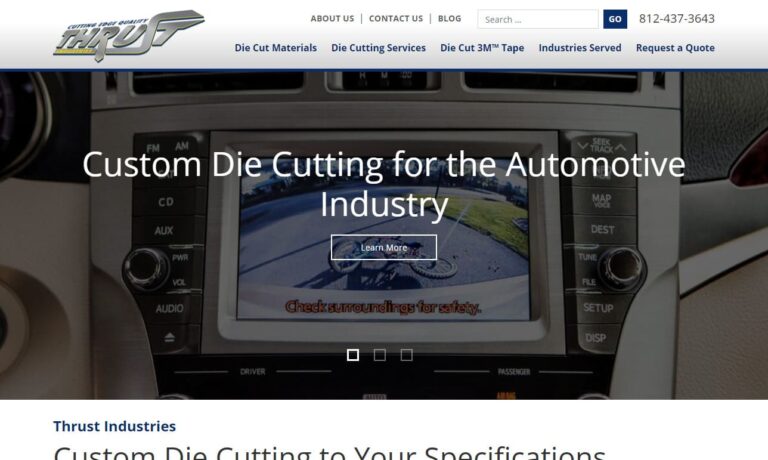
At Garland Manufacturing Company, we take pride in our expertise in plastic fabrication, delivering innovative solutions tailored to meet the needs of diverse industries. Our commitment to precision and quality drives every aspect of our work, from the initial design phase to the final production. We excel in crafting high-performance plastic components.
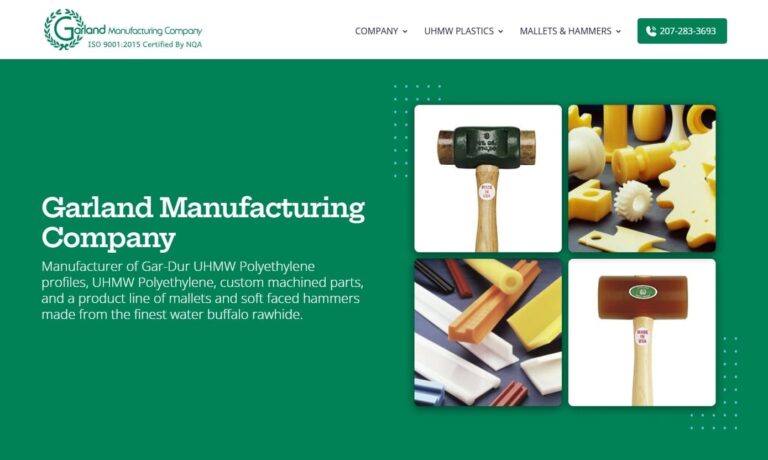
More Plastic Fabricator Companies
Types of Plastic Fabricators
Plastic may be a versatile and long-lasting material. There are numerous plastic production techniques, and a few will be covered below.
Plastic Welding
Plastic welding uses heat to fuse multiple workpieces together, similar to metal welding. This method works well with thermoplastics that can't be bound with adhesive. However, particularly if workpieces have considerably different melting points, individual pieces may be bonded with a filler material in between. Welding techniques include spinning, high-frequency vibration, and contact welding. Different techniques use different equipment and work well with different types of plastic.

Plastic Compounding
Plastic compounding is mixing two different kinds of plastic before forming a single object. Molten polymers are created with a mold and a die and precisely mixed before forming. Compounding is used to simplify processing or improve a product's performance. Compounding allows manufacturers to benefit from the strengths of multiple plastics by creating new materials for specific applications.
Plastic Thermoforming
Plastic thermoforming has two main processes: vacuum thermoforming and pressure thermoforming. In both procedures, plastic sheets are heated, stretched over a mold, pressed into the mold, and extra plastic is cut. In pressure thermoforming, manufacturers apply pressure to the top of the plastic workpiece. This forces air out of the gap and creates the desired shape in the mold. In contrast, vacuum thermoforming sucks all the air out of the space between the softened plastic and the mold. Pressure forming is more precise; it captures more texture and fine details.

Thermoforming allows manufacturers to produce large volumes at affordable prices without sacrificing craftsmanship. However, there are restrictions on how complex parts can be, which only apply to thin-walled goods. Furthermore, pieces need to be trimmed, although some manufacturers recycle trim.
Plastic Extrusion
Plastic extrusion is used to make tubing, piping, or sheet components. Plastic extrusion makes future processes, like forming or processing, easier. For instance, adhesion or lamination processes usually require a piece to undergo plastic extrusion first. The most common extrusion methods are profile extrusion and film extrusion.
Plastic extrusion begins by melting plastic pellets. A pressured screw mechanism forces the molten plastic into a die. The plastic solidifies around a calibration sleeve to create a pipe or tube component with a specified diameter. Sheet extrusion produces thin plastic sheeting using a similar method.

Plastic Foaming
Products made of foam can be molded into different shapes, like egg cartons or package padding. Round, sheet and film are examples of common foaming configurations. Polymer composites are formed through chemical or physical blowing to acquire the necessary features. Like compounding, the base material can be enhanced with additives like colors, antioxidants, and fire retardants. Polyethylene, polypropylene, polyamide, and plasticized PVC are examples of materials that can foam plastics. Chemical reactions can also turn thermosets into foam padding for furnishings or other uses.

Plastic Lamination
Plastic lamination creates a barrier is made along the top of another material. Lamination increases the longevity, styling, or appearance of a product. In addition, lamination can protect a delicate or easily degradable material and is a cost-effective way of preventing future maintenance.

Benefits of Plastic Fabrication
The manufacturing process of plastic fabrication is flexible, effective, and simple. A few of the advantages are listed below.
- Ease of formation: Other common materials have a higher melting point than plastic. Plastic can easily create complex geometries due to low melting temperatures and strong malleability.
- Rapid production: plastic molding is a relatively quick process. Manufacturers who use plastic fabrication processes have faster lead times and faster production rates.
Choosing the Correct Plastic Fabricator
To ensure you have the most constructive outcome when choosing a plastic fabricator, it is important to compare several companies using our directory of plastic fabricators. Each plastic fabricator has a business profile page highlighting their areas of experience and capabilities, along with a contact form to directly communicate with them for more information or request a quote. Review each plastic fabricator business website using our patented website previewer to quickly learn what each company specializes in. Then, use our simple RFQ form to contact multiple plastic fabricator companies with the same form.