Plastic is a versatile, inexpensive, long-lasting material that can be formed into any shape and has a wide range of properties that suit different applications. Read More…
We are accomplished plastic fabricators. The usability of our products is unmatched. We offer a plethora of secondary services for optional features. All of engineers are extremely thorough when creating these plastics. Your satisfaction is essential to us. You can count on us to give you exactly what you are looking for. Give us a call today to learn more information!
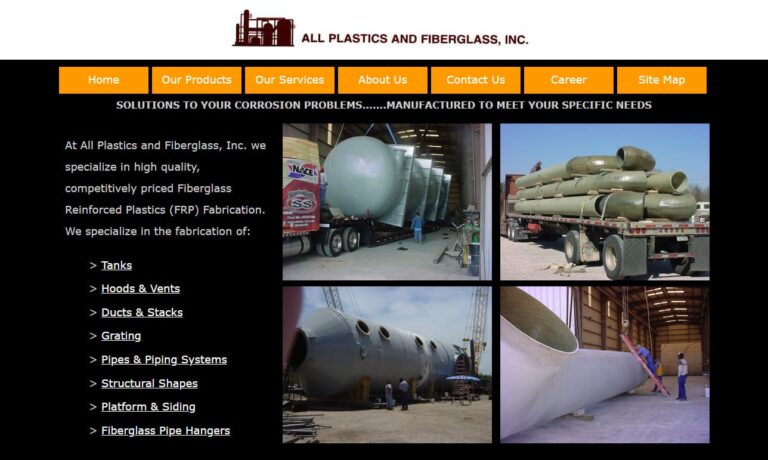
At Park Plastic Products our main focus is manufacturing custom fabricated tanks from polypropylene and co-polymer. Chemical rinse tanks, dip tanks, anodizing tanks, tank liners, air purification tanks, drip pans and custom rolled polypropylene tanks are available to be built to your size and specifications.
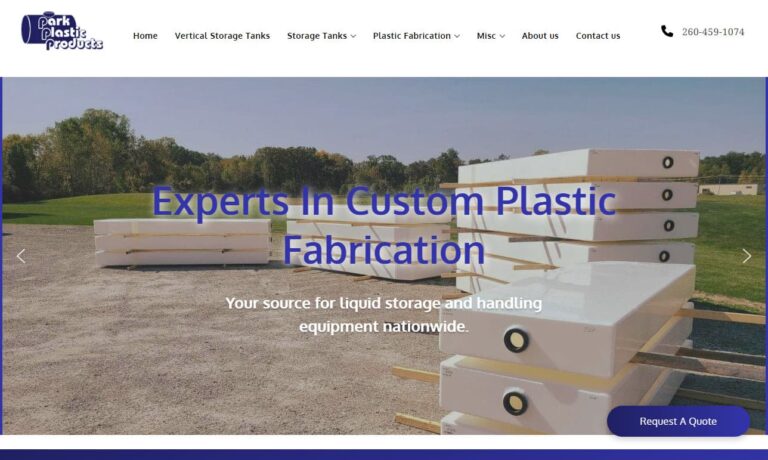
Experts in unique custom plastic extrusion products and complex secondary fabrications, Northland Plastics specializes in custom plastic profile extrusions such as extruded plastic tubing, rigid plastic profiles and flexible plastic profiles. Call Northland Plastics, Inc. for all your extrusion needs.
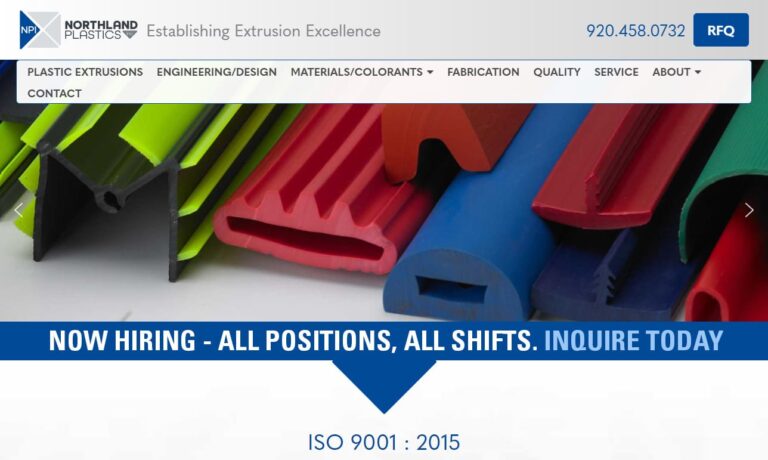
Thrust Industries is committed to quality in everything it does, from its technical knowledge to its customer service. As a leading plastic fabricator, the entire team at Thrust is devoted to developing high-quality solutions for your business and delivering them exactly when you need them. Thrust has served the needs of customers across the globe for over 3 decades— become one of them today.
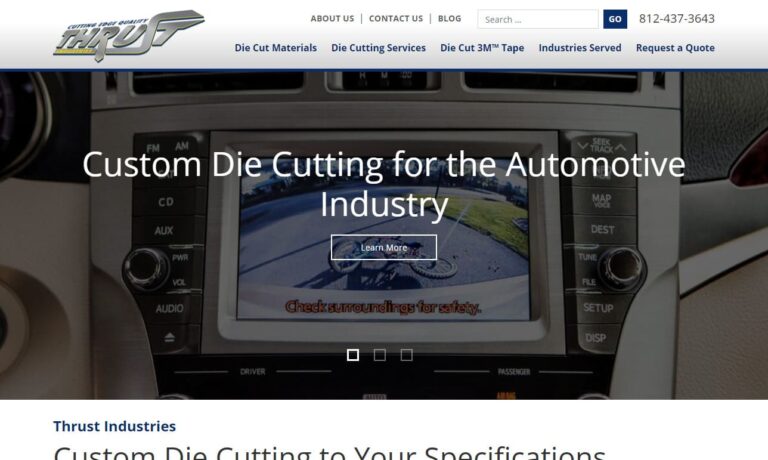
At Garland Manufacturing Company, we take pride in our expertise in plastic fabrication, delivering innovative solutions tailored to meet the needs of diverse industries. Our commitment to precision and quality drives every aspect of our work, from the initial design phase to the final production. We excel in crafting high-performance plastic components.
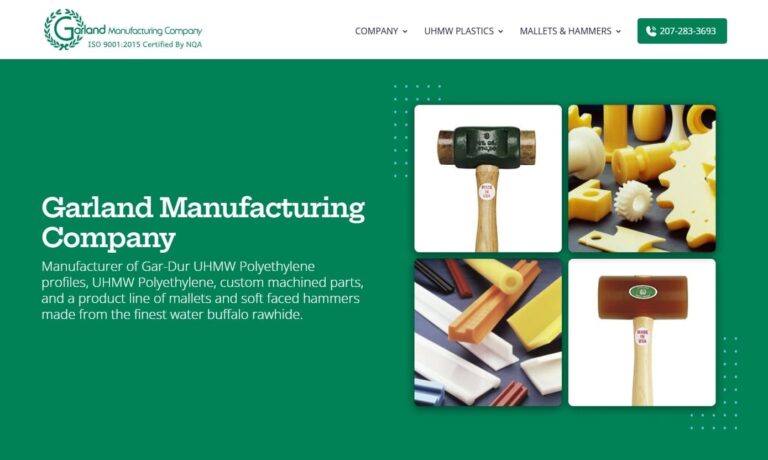
More Plastic Component Companies
There are many different kinds of plastic, each with their own defining characteristics, limitations and benefits; these include acrylic, nylon, polyester, polycarbonate, polypropylene, polyvinyl chloride, polystyrene and polyethylene. Each of these is a pure plastic resin base that is melted and mixed with additives that change or enhance the plastic's properties, such as strength, temperature, chemical, moisture and abrasion resistance, durability, flexibility, hardness, ductility, lifespan, texture, surface finish and color.
All these materials are considered thermoplastics and are easily formable when heated until pliable or molten. In order to form components, plastic may be molded, cut, welded, bent/formed, stamped, milled, annealed or lathed. Most of these processes are automated and done in high volumes, which decreases the cost. The food and beverage, automotive, appliance, electronics, pharmaceutical, construction, plumbing, oil, packaging, aerospace, sports equipment and cosmetics industries, among many others, use plastic components everyday. In an industrial setting, many plastic parts like gaskets, fasteners and washers are important components of manufacturing machinery.
There are three main ways to form plastic into a component: molding, forming and assembling. Molding involves a metal mold in the shape of the desired product and heated molten or malleable plastic that forms to its shape. Some plastic molding processes involve a vacuum that ensures an air-tight fit around the mold. These products are usually larger in size and flat or hollow in form.
Plastic molding is the preferred way of fabricating complex plastic products. Flat, simple parts are formed by a couple of different processes. These include stamping, where a heavy metal ram forces a mold to cut out pieces from a flat sheet of plastic. Other plastic forming methods that produce flat components include laser cutting and die cutting, which use a high beam of concentrated light to melt away the plastic or a sharp metal needle or saw.
Many flat plastic parts require assembly in order to form a finished product. The most common way to assemble plastic is by plastic welding, a process that involves heating the edges of two plastic pieces until they have melted or softened, and pushing them together. They form a watertight seal and permanently join together to form a single part.